Precision reverse engineering for KEO’s beer wheat mill
KEO | 2024
Rapid prototyping
Design for Manufacture (DfM)
Detailed design
Production validation
Challenge
KEO needed a highly accurate 3D model of a spare part to ensure successful manufacturing. The challenge was to scan, reconstruct, and optimize the part while coordinating material analysis with the University of Cyprus and gathering competitive manufacturing quotes.
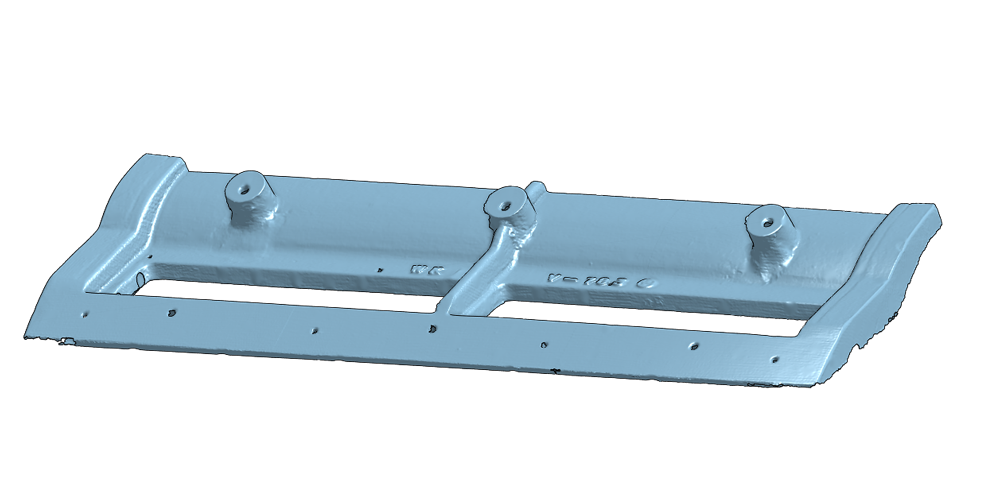
Approach
We followed a structured reverse engineering process to deliver precise and manufacturable results:
- 3D Scanning: Captured high-resolution scans, processed the data, and created an accurate mesh model.
- Reverse Engineering: Converted the mesh into a solid CAD model, refining critical areas for better performance.
- Manufacturing Feasibility: Engaged machine shops for pricing and timelines, ensuring cost-effective production.
- Material Analysis: Partnered with the University of Cyprus for in-depth material characterization.
By combining advanced scanning, CAD modeling, and manufacturing coordination, we ensured a high-quality, production-ready solution for KEO.
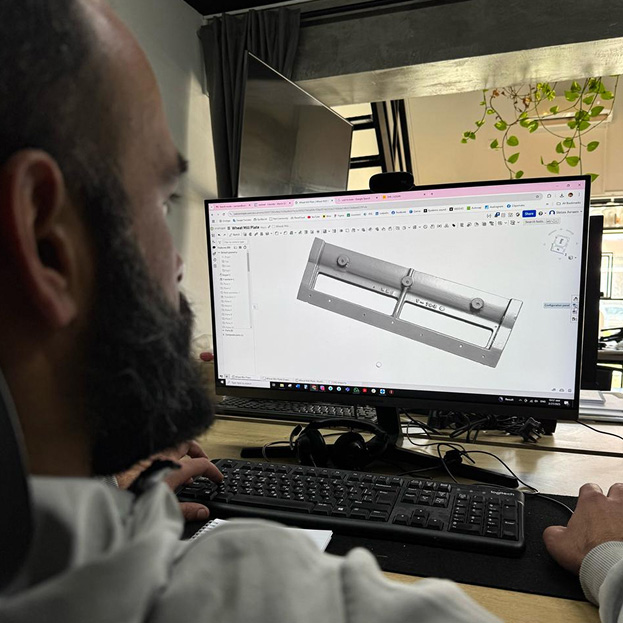
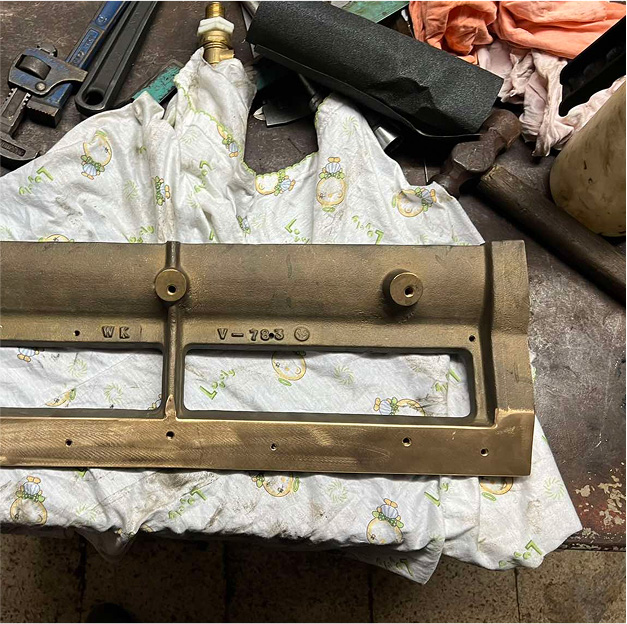
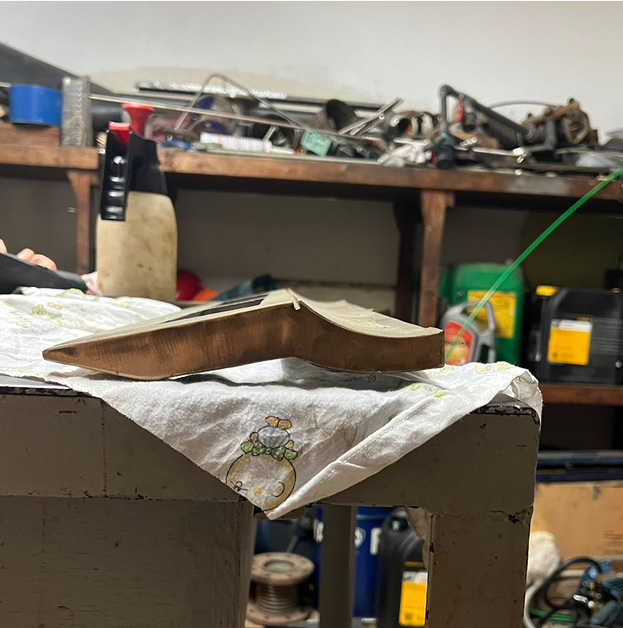
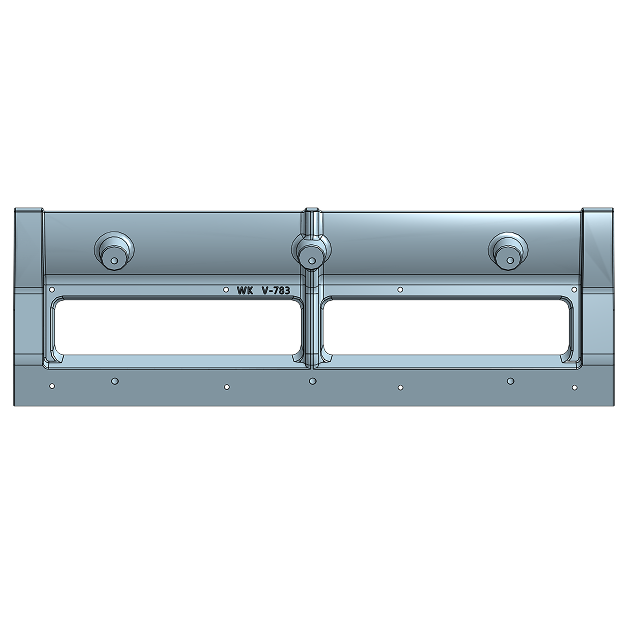
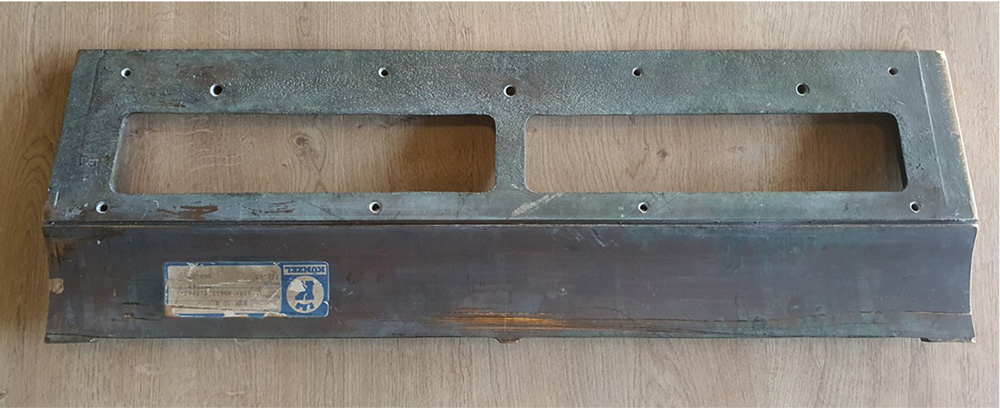
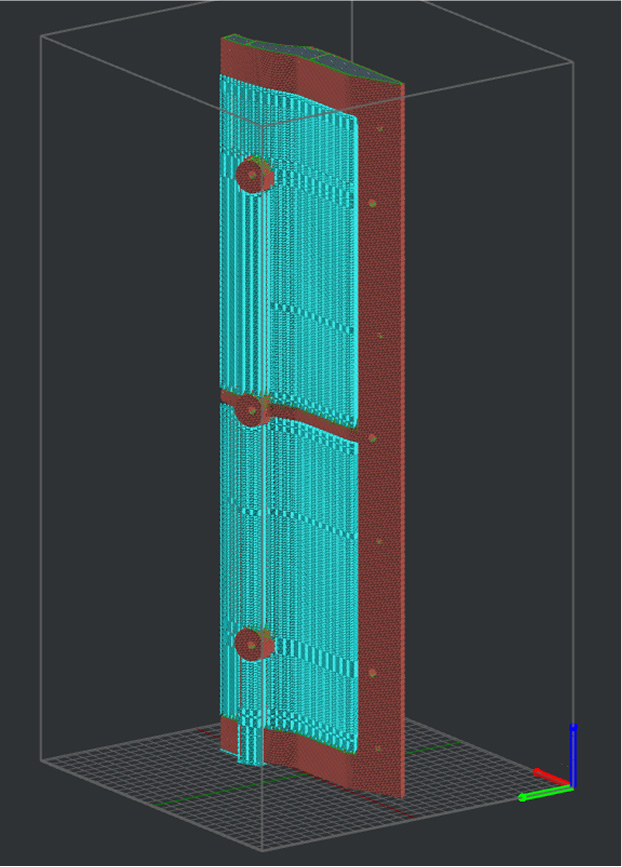
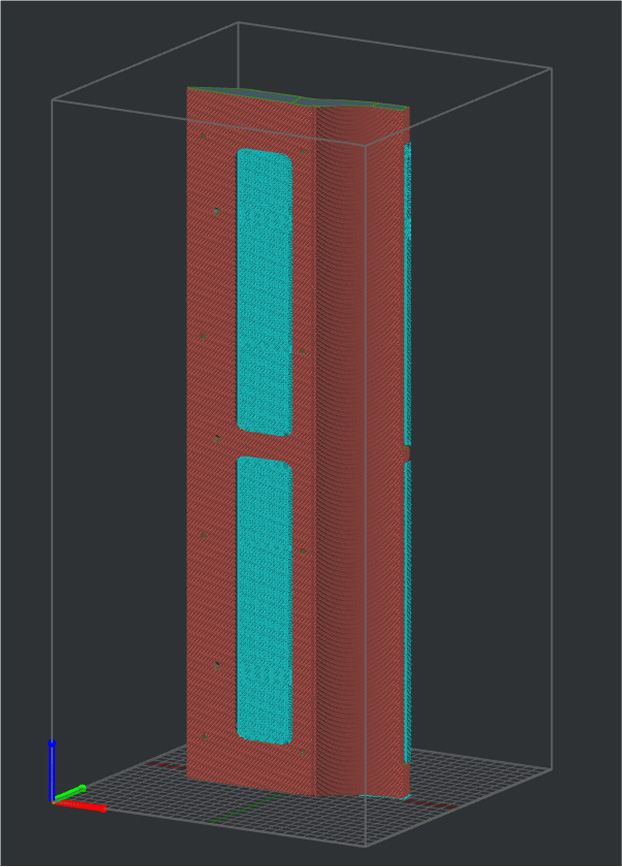
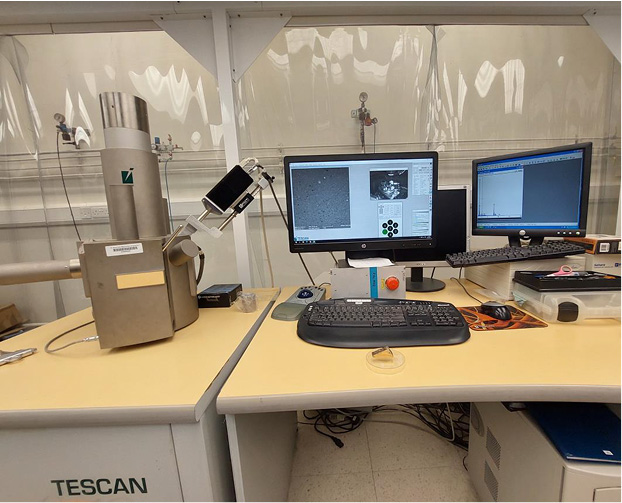
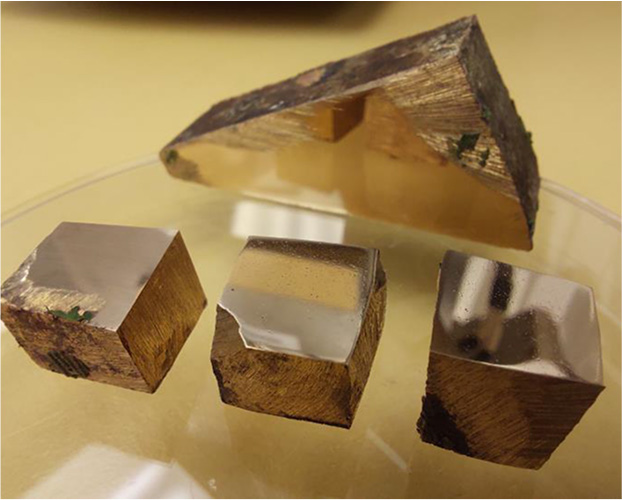
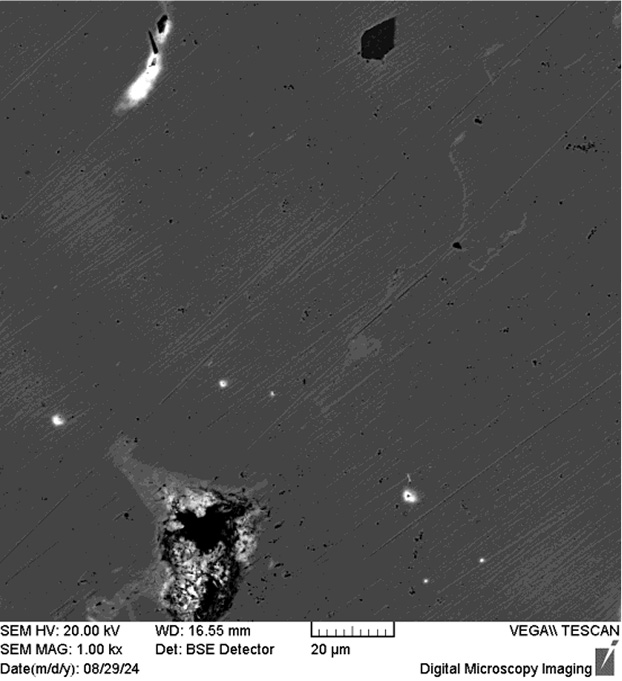
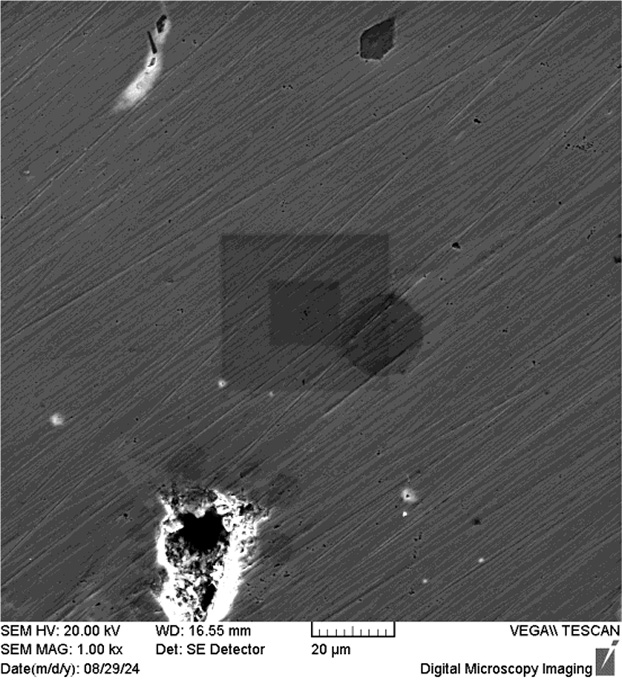
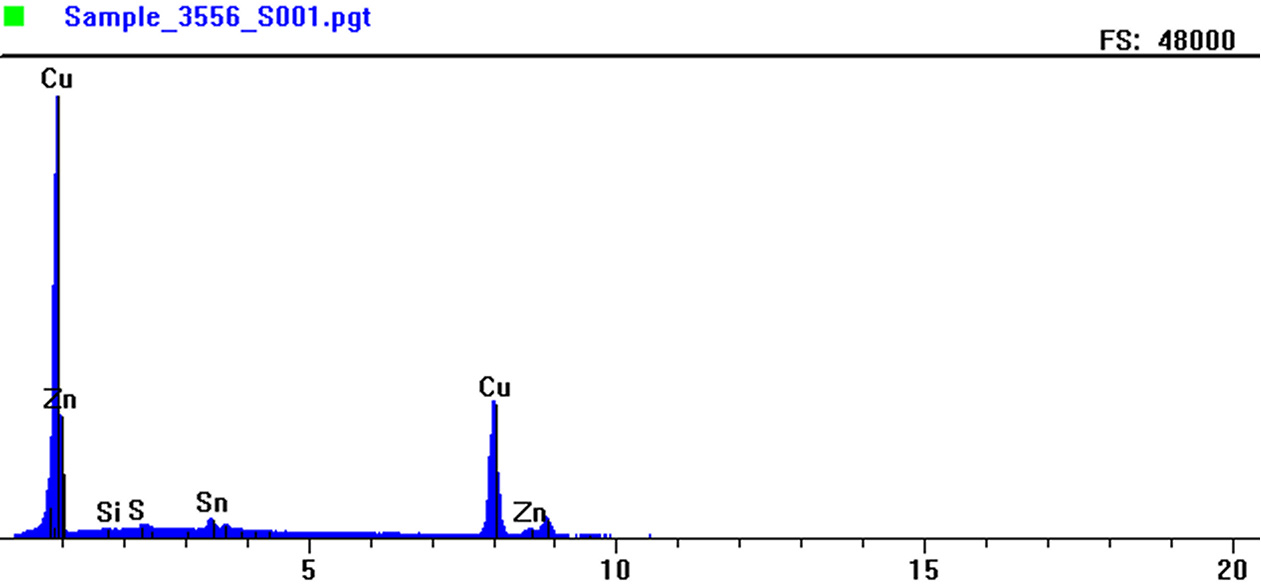
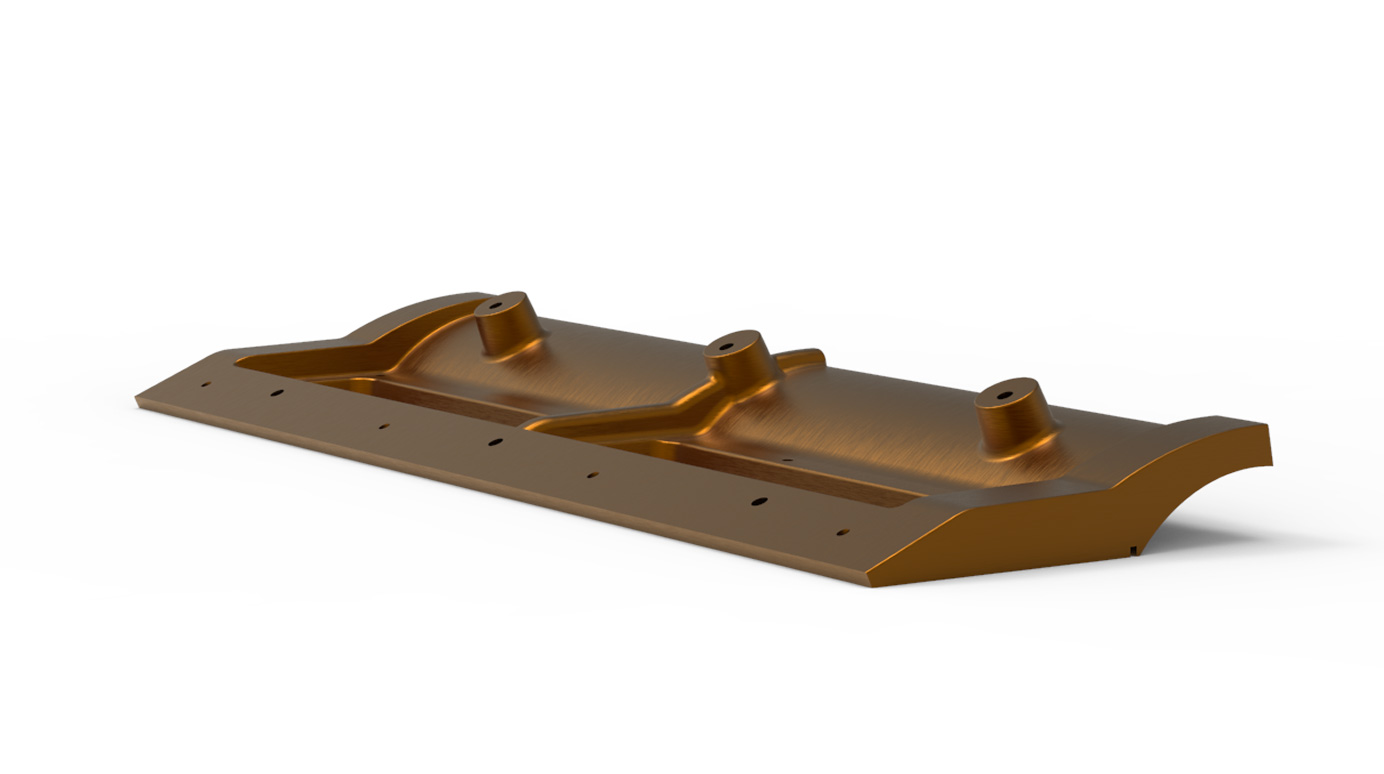
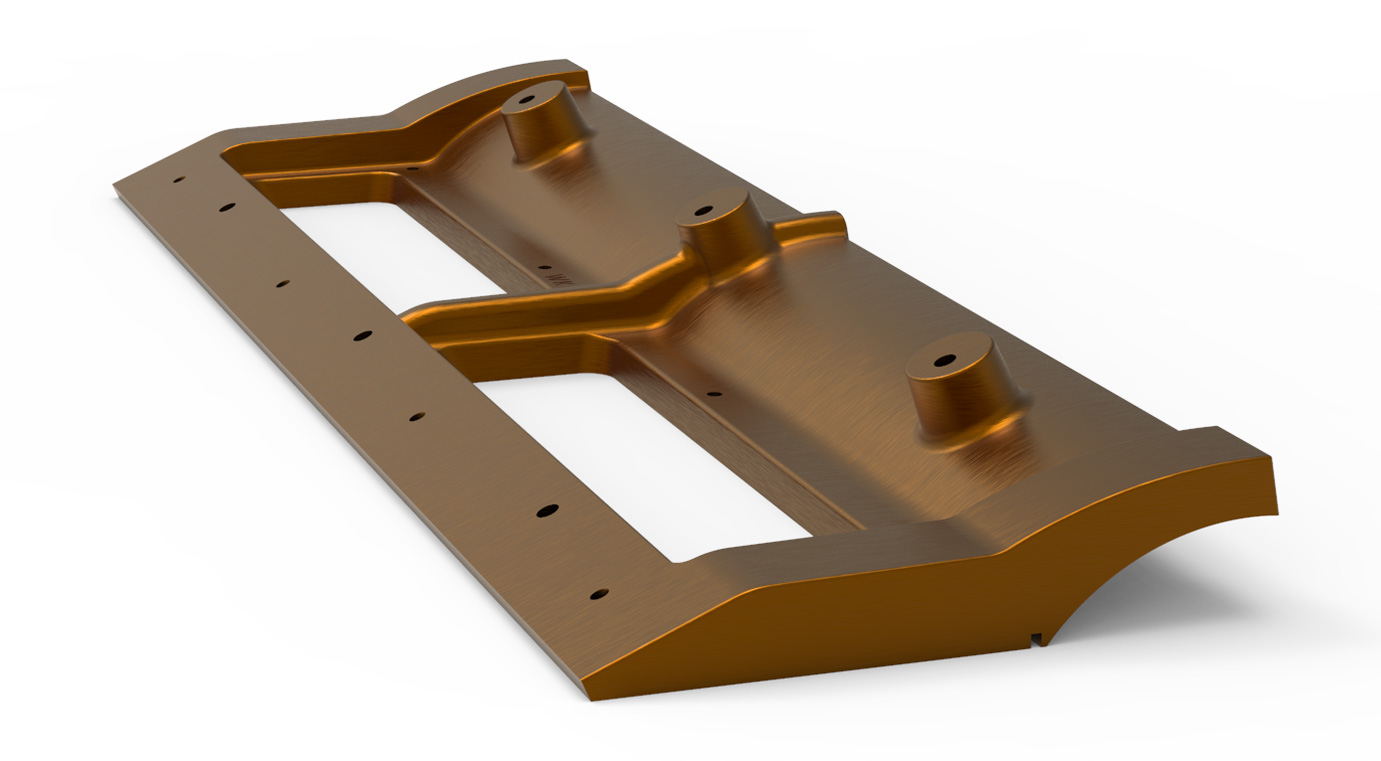